Carpeting
In Bellevue, Washington
We can't wait to help you explore the soothing carpet styles for your inspired home. Visit Carpet To Go in Bellevue, WA, and browse our extensive carpet selection. We serve greater Seattle as well!
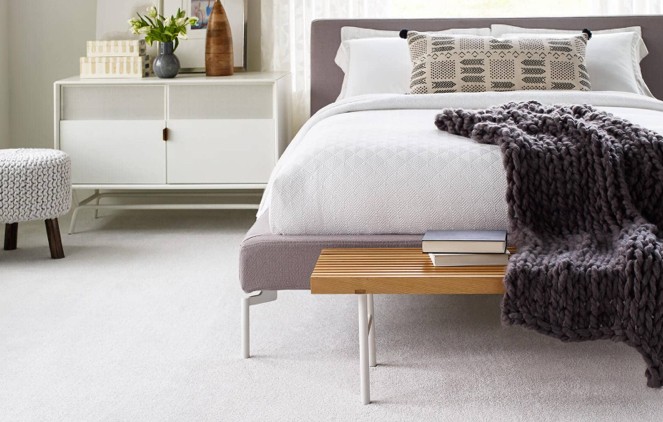
SOFT AND COMFORTING, YOUR FAMILY WILL LOVE NEW CARPET!
Nothing brings in the relaxing warmth and supreme softness to your bedrooms and living rooms like exceptional carpet. Whether it's creating a sanctuary for unwinding or a cozy space for family time, the perfect carpet style awaits! Explore our plush nylon and stain-resistant woolen carpets to elevate the comfort and style of your home.
Shop Carpets Now!
Browse our extensive carpet catalog today!
We Carry The Top Name Brands In Carpet
When you want to elevate your interior spaces, your home deserves the very best. Carpet To Go carries the most trusted carpet brands for the top quality that you can rely on.
Why Choose Carpet?
For creating a warm, inviting, and comfortable atmosphere, carpet may be the ideal flooring choice for a number of impressive reasons. Soft carpet can be a safe landing place for energetic little ones and a great surface for family game nights. With the thundering footsteps of kids and pets running through the home, stain-resistant and easy-to-clean carpet varieties can provide extra sound absorption and a quieter overall atmosphere. Additionally, carpet offers a versatile flooring solution for various applications, including residential spaces, commercial properties, and even indoor/outdoor areas.
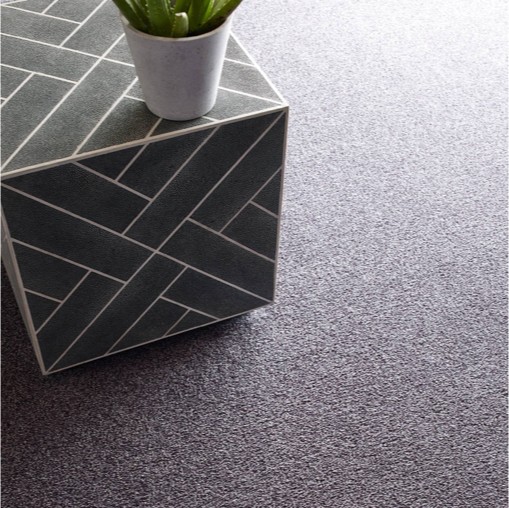
Types of Carpet
In addition to the wide range of gorgeous carpet shades that you can select from, there is a vast amount of carpet constructions, textures, and patterns that you can bring home. Depending on your specific household factors such as overall activity, kids, pets, and level of your home, different types of carpet will be better suited for your rooms than others.
Explore Carpet Styles
With so many carpet types to choose from, finding the perfect style for your space is easy! Carpet To Go offers a wide variety of carpet styles, including:
Frieze: Known for its twisted fibers that create a textured appearance, Frieze carpet offers excellent durability and hides footprints well.
Berber: Featuring looped fibers, Berber carpet provides a classic look and is known for its high resistance to wear and tear.
Patterned: From intricate florals to bold geometric designs, patterned carpet adds a touch of personality and style to any room.
Textured: Textured carpet offers a unique visual appeal and can help hide imperfections in subfloors.
Unsure Which Carpet Style is Right for You?
Get a Free Quote! Let our experts help you find the ideal carpet for your home!
Carpet Installation
After you have been through the process of carefully selecting your new favorite carpet styles, there’s no need to feel overwhelmed by the carpet installation process. The Carpet To Go experts can help you prepare before, during, and after your new carpet installation. Now it’s time to prepare for your stylish new flooring!
Carpet Care Experts In Bellevue, WA
Now that you have your new carpet installed, it’s time to keep your rooms looking stunning for as long as possible! The key to being ready for any mishaps that can occur at a moment’s notice is to know the proper carpet care steps for each situation. From preventative steps and proper regular care to stain removal procedures, it always helps to be prepared. Always refer to the manufacturer's warranty for care instructions.
Carpet FAQs
Carpet fibers are the foundation of any carpet, and they come in a variety of materials, each with its own unique characteristics. Some of the most common carpet fibers include:
- Nylon: Known for its durability, stain resistance, and versatility, nylon is a popular choice for high-traffic areas.
- Polyester: Polyester is another durable option that offers good stain resistance and a wide range of colors.
- Wool: Wool carpets are luxurious and soft to the touch, providing excellent insulation and sound absorption.
- Triexta: A newer fiber that combines the durability of nylon with the softness of wool, triexta offers a great balance of performance and comfort.
To prolong the life of your carpet, go beyond basic cleaning and maintenance. Schedule regular professional cleanings, use furniture pads and rugs in high-traffic areas, and encourage people to remove their shoes before entering your home. By taking these proactive steps, you can help prevent carpet wear and tear and maintain its appearance for years to come.
The lifespan of carpet can vary depending on factors such as the type of fiber, quality, and level of foot traffic. With proper care and maintenance, well-made carpet can last up to 15 years or more.